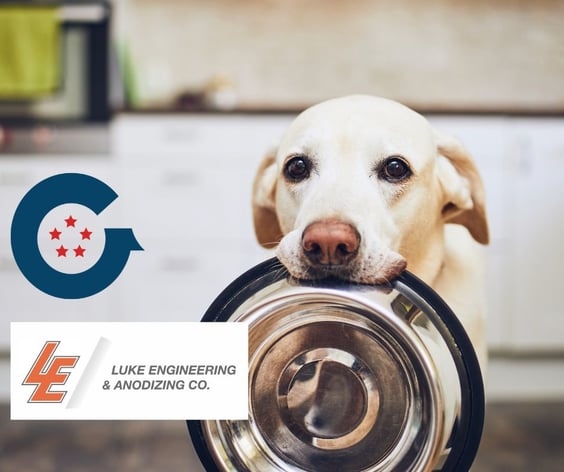
Protecting your casted investment “organically” with anodizing
Protecting your casted investment “organically” with anodizing
In part 5 of this series, we will learn about anodizing, the different types, and benefits. Thanks to Luke Engineering & Anodizing Company in Wadsworth, Ohio for providing the detailed information for this article describing the anodizing process and its benefits to protecting your die casting.
Anodizing
Your casting can smile once protected with an anodized coating
You’ll recall from the first article in our “Care and Feeding,” series, that aluminum oxidation and corrosion are not synonymous. It’s precisely the aluminum oxide layer that creates its corrosion resistance. The anodizing process exploits this fact by intentionally forming a controlled layer of aluminum oxide on the surface.
Anodizing is the electrochemical conversion of aluminum to aluminum oxide. The oxide coating is created by placing an aluminum part in a sulfuric acid bath while running a low-voltage DC current through the part to cathodes in the tank. The casting plays the role of the anode in the electrical circuit and the oxide layer begins to build.
Anodized and uncoated casting
Anodizing forms a coating that is durable, non-conductive, abrasion-resistant, and offers excellent corrosion protection. It is also an excellent primer for paint or powder coat.
Types of Aluminum Anodizing
The most common specification for anodized aluminum die castings are MIL-A-8625 Type II, Class 1 & 2, or Type IIB (a thinner coating).
The typical thickness for these coatings are:
Type II, Class 1 (Undyed) is 0.0004” – 0.0006”
Type II, Class 2 (Dyed) is 0.0007 – 0.0012”.
From a dimensional perspective, anodizing is a conversion coating where the outer aluminum surface is converted to the anodized oxide layer, with penetration into the surface and build up onto the surface. A general rule of thumb is 50% penetration and 50% build-up, so a coating of 0.001” would be close to 0.0005” penetration and 0.0005” build-up on each surface.
“Thickness” is typically referred to as the overall aluminum oxide coating applied, while “Build-up” is referred to the dimensional growth upon the original surface.
Dyes can be used to create sharp, bright colors on many aluminum materials such as 6061. Unfortunately, the silicon in the die casting alloy makes colored dyes ineffective. Most aluminum die castings are either undyed, which creates a greenish finish or Dyed Black.
Hard Anodizing
Hard anodizing, referred to as Type III anodizing, is a denser, thicker, version of Type II Type II Anodizing. A typical coating is 0.002” +/- 0.0004” thick. This anodic film gives aluminum parts superior abrasion and corrosion resistance while retaining the numerous advantages inherent to aluminum. With one of the largest process tanks in the country (10’ x 8’ x 7’), Luke Engineering has been able to successfully hard coat parts used in space, defense, and medical industries. Combined with our top-notch computer-controlled Quality System, we can hold tolerances as close as +/- 10%. Unfortunately, the traditional Hard Anodizing Process cannot be successfully applied to a die casting. Until now.
Lukon DC (Hardcoat for Aluminum Die-Castings)
It is a popular misconception that hard anodizing of high-pressure aluminum die-castings is nearly impossible. However, at Luke Engineering, we have revolutionary technological developments involving modified electrolyte chemistry and unique, computer-generated electrical waveforms that permit the application of much thicker and more abrasion-resistant hard anodic coatings. Lukon DC is a proprietary hard coat process developed to form thick, hard anodic coatings on high-pressure aluminum die-castings. High levels of alloying elements in die-castings, particularly silicon and copper, interfere with the normal formation of anodic coatings. Normal commercial hard anodizing processes form only thin, soft coatings. With Lukon DC, the electrolyte and electrical waveforms are modified to compensate for the lower aluminum and high alloy levels. This allows for the formation of thicker and harder anodic coatings than previously thought possible. With these coating improvements, aluminum die-castings can now be successfully used in applications where cost-effective wear resistance is a requirement. Current and potential applications include brake, transmission, and hydraulic pistons, housings, and covers, as well as sheaves and pulleys.
Chromate Conversion
Chromate Finish vs Raw Casting
Unlike anodic coatings, Chemical Conversion Coatings create a surface that maintains conductivity while resisting corrosion, especially corrosion caused by moisture. Conversion coatings are used primarily as a paint preparation or as temporary corrosion protection. These coatings are also used as low electrical resistance, protective coating on areas masked from non-conductive anodize. It is difficult to detect a chromate coating on a die casting. The casting with the chromate coating in the picture is slightly darker than the raw part.
Now that we have a complete understanding of the various finishing processes available for high pressure die castings, we will put them to the test. We are currently performing a salt spray test on identical castings with all the coatings described in this series. Subscribe to our blog to learn which coating is really the best at protecting your die casting.
If you’re looking to give your components a competitive edge and greatly extend their longevity, or just want to learn more about what’s possible with this process, don’t hesitate to contact Luke Engineering. They’re ready to help you figure out if Lukon DC might be right for you.