Protecting your aluminum die cast investment “organically” Electrocoat and Liquid Coatings
In part 3 of our series, we will learn about the benefits and challenges of applying E-Coat and Liquid Coat to aluminum die castings. Thanks to George Giering, of Giering Metal Finishing, Inc. in Hamden and Waterbury, CT for providing the content for this article.
Electrocoat
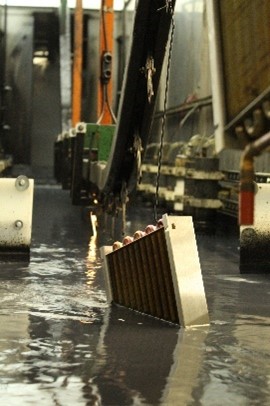
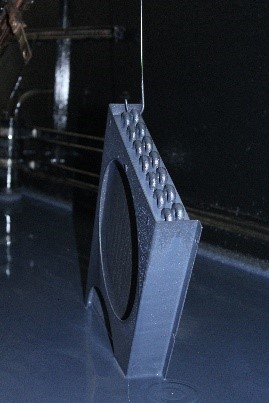
Electrocoat, also known as E-coat, is very similar to electroplating. Instead of depositing metal, e-coat deposits an organic liquid resin bound to a colored pigment over the aluminum die cast part surface using electro current.
The automotive industry developed e-Coat in the late 1980s. It is the reason why cars have become much more resistant to rust. Electrocoat is very popular in the automotive and military industries because, like plating, it deposits a uniform protective film over 100% of the surface. Electrocoat is very environmentally friendly with close to 0% emissions, is non-hazardous, and is the most efficient coating with almost zero waste.
The E- coat deposition process can be precisely controlled. This allows much thinner coatings than powder coating. This makes e-coat an ideal primer, although it is often used as a final finish. A top coat of enamel or powder can be applied over the E-Coat to provide a durable and attractive finish.
There is two different application technologies for E-coat; anodic and cathodic deposition. Anodic brings the part to the paint which is simpler and is often used for cosmetic applications. Cathodic brings the paint to the part, encapsulating the part for superior corrosion protection.
Much like powder coatings, custom chemistries can be created to suit the application. The two primary chemistries are epoxy and acrylic. Epoxy electrocoat offers excellent protection against mechanical abrasion and harmful chemicals. Acrylic is used for outdoor applications where UV protection is required.
E-coat resin is thermoset. This means that when it is cured, it becomes bonded and irreversibly hardened. This creates a surface that is very difficult to damage.
Liquid Coatings
Liquid coating refers to the traditional finishing application of wet paint. There are still many uses for wet spray applications:
- Custom finish colors unable to achieve via powder coating (like for autobody)
- Specific texture patterns unique to paint: soft suede finishes, wood coatings, plastic coatings, and other non-bakeable material finishes
Liquid paints offer the widest array of colors in any gloss (Pantone Matching System (PMS), Munsell, RAL & more) and can be easily mixed in small quantities for custom appearances. This is a great advantage over powder coating which requires large batches at expensive prices.
Two categories of liquid coatings are solvent-borne and water-borne. This refers to the element used to dissolve the coating into a liquid for easy application.
Solvent-borne liquid coatings are very forgiving on castings because the solvent “bites” onto the surface and can be cured at very low temperatures.
Waterborne liquid coatings require a high-temperature cure but are great options for parts requiring high tolerance.
Liquid coating systems can be smooth or textured. Textures can be applied in a variety of sizes ranging from fine to rough textures. The texturizing process is a two-step process; first, a smooth base layer of paint is applied as a foundation followed by a subsequent topcoat layer of texture accomplished by changing spray air pressure and lowering the viscosity of the paint.
Combining Organic and In-Organic coatings – the ultimate protection
Organic and inorganic coatings can be combined to provide amazing protection. We have experienced fantastic results by applying a weatherable polyester powder coat over an anodized finish. Anodizing pre-treatment is also very aggressive and assists in removing mold release from the surface to assure perfect adhesion of the powder coat to the casting.
We will learn all about anodizing in part 5 of our series. But first, we will discover the importance of having a high-quality casting that is properly pretreated to obtain that perfect finish. Subscribe to our blog to learn more!